Sterilization devices
Laboklav 55-195
FLEXIBLE SOLUTIONS FOR HIGH DEMANDS.
The steam sterilizer is available in two chamber diameter options: Ø 400 mm (models 55, 80, and 100) or Ø 500 mm (models 135, 160, and 195). It can be configured both horizontally and vertically, depending on the spatial constraints and requirements of the installation site. With a power range of 3.3 to 10 kW, the sterilizers are suitable for a variety of applications, from smaller to more extensive sterilization tasks. The flexible design and powerful performance make it a versatile solution in sterilization technology.
Selected chamber diameter:
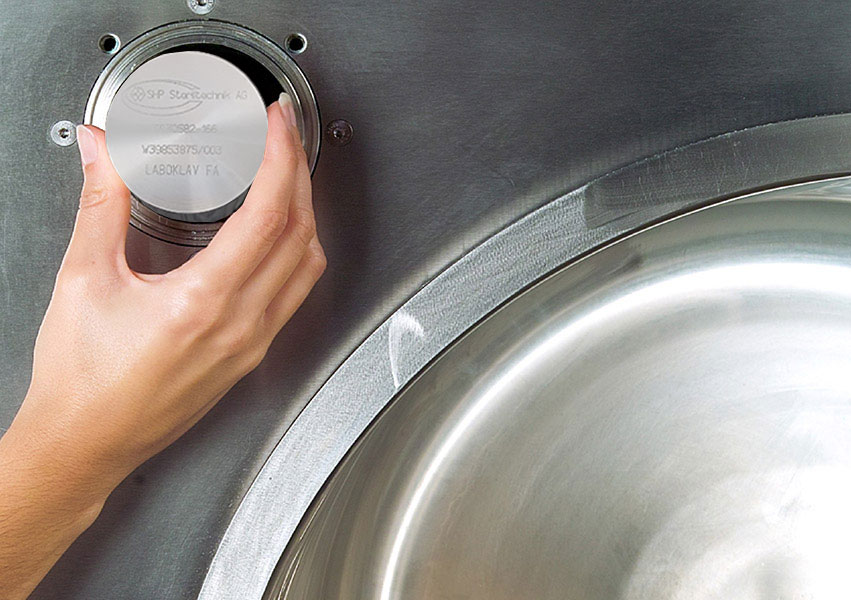
Laboklav 55-195
upgrade levels and additional components for the steam sterilizer series
Our program includes: touchscreen control with integrated documentation and archiving function, which is network-capable and uses the documentation software SegoSoft. Various options are available for rapid cooling of liquids. The vacuum system ensures optimal conditions, while exhaust filtration is required according to safety level S2. All casing panels and cover hoods can be made entirely of stainless steel.
Option M: Fast recooling
(without counter pressure, for open vessels)
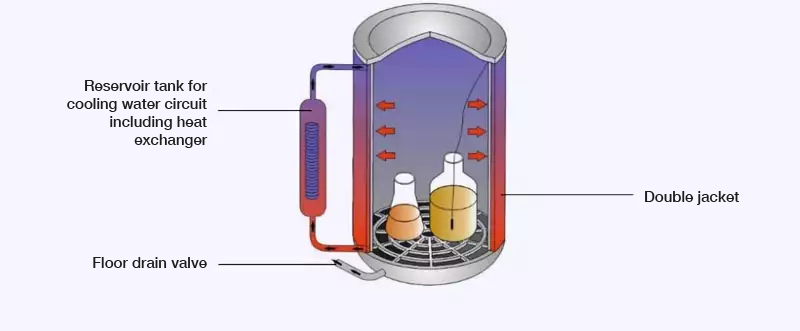
The Laboklav 55-195 series can optionally be equipped with a highly effective recooling device for liquids. During the cooling phase, cold DI water is circulated around the chamber via the double jacket, achieving accelerated cooling of the liquids. As a result, the cooling phase can be reduced by up to 50%*. The crucial criterion here is the double jacket, which, unlike a cooling coil, ensures full-surface cooling of the chamber and rapid heat removal. The cooling system is supplied from the integrated storage tank in the autoclave. After flowing around the chamber, the DI water is returned to the tank. The absorbed heat is released to the cold water required for steam condensation via a heat exchanger and discharged into the wastewater via the collection connection.
Conventional cooling systems in autoclaves require approximately 50 liters of DI water or more* per cycle. This expensive DI water is discarded. The Laboklav recooling system leads to significant savings in operating costs and makes a valuable contribution to environmentally friendly resource management.
During the cooling phase, a liquid loss of approximately 5-8% can be expected. This cannot be avoided physically. If liquid loss is unacceptable, we recommend the cooling options with back pressure (S), possibly in combination with a radial fan (L).
* depending on bottle size and load volume
Option S: Counter pressure
(for open vessels) only in connection with Option M
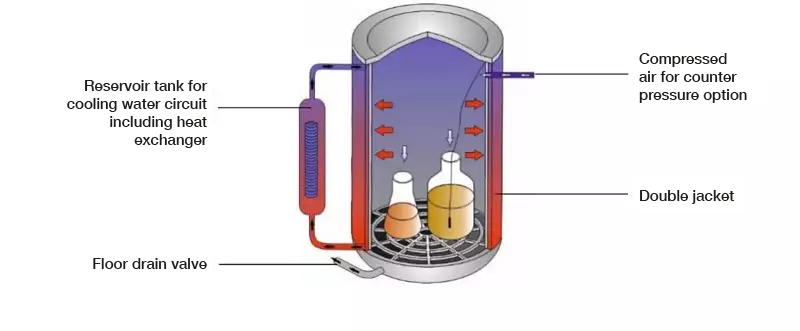
The integrated back pressure device extends the rapid recooling (Option M). Sterile filtered compressed air is introduced into the chamber, ensuring that no liquid loss can occur during sterilization. The chamber is maintained at a higher pressure than the pressure present in the vessels, thereby effectively preventing evaporation losses. An external compressed air connection is required for this purpose.
Option L: Radial fan
(for tightly sealed vessels) only in connection with Options M and S
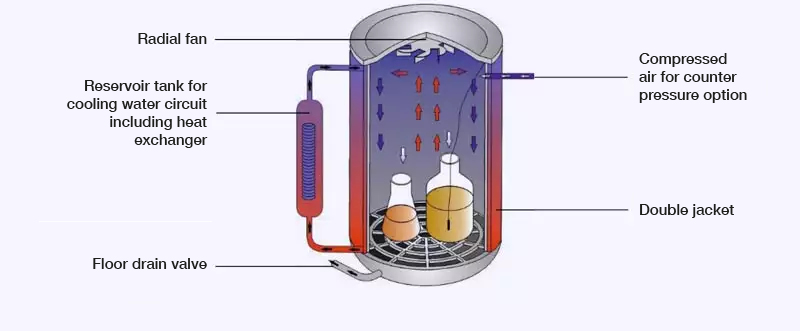
The radial fan complements the enhanced cooling programs with counter pressure (Options M and S) and enables the sterilization of pressure-tight sealed vessels. The built-in fan effectively prevents temperature stratification and ensures forced convection within the chamber. This effectively prevents bursting of tightly sealed containers. Additionally, during the cooling phase, heat dissipation is improved, and cooling performance is significantly increased.
SegoSoft
SegoSoft - the fully automated, digital batch and process documentation for your sterilizers, thermal disinfectors, and sealing devices.
stainless steel
Casing panels and cover hoods completely made of stainless steel.
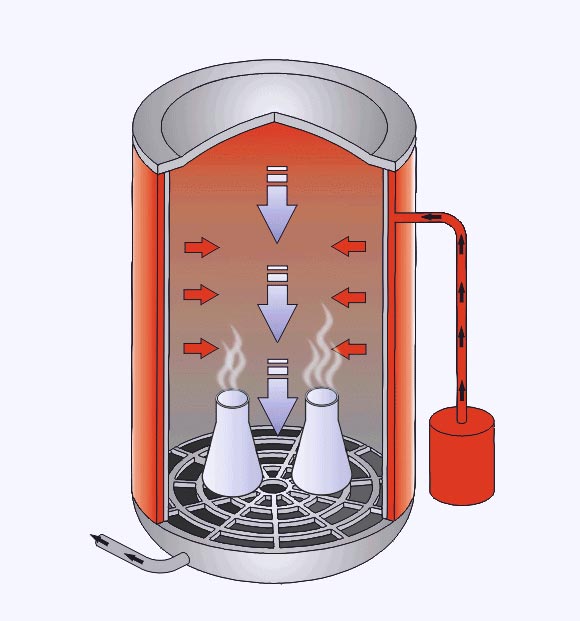
Option V: Pre-vacuum and drying vacuum
The Laboklav 55-195 series can optionally be equipped with extensive vacuum options.
Pre-vacuum (continuous or fractionated):
A pre-vacuum primarily serves for proper degassing of packaged sterilization goods of all kinds, solid and moist waste in bags, as well as other goods that are difficult to degas. A multi-stage (fractionated) pre-vacuum reliably removes existing air and allows unimpeded penetration of steam to the sterilization goods. Only with fractionated pre-vacuum are reproducible sterilization results according to DIN 58951-2 ensured for the mentioned applications!Drying vacuum:
The drying vacuum is required for the post-drying of all packaged sterilization goods. During the drying phase, the condensate present in the packages is reliably evaporated and removed from the chamber by vacuum. This avoids additional handling and post-drying in a drying cabinet.
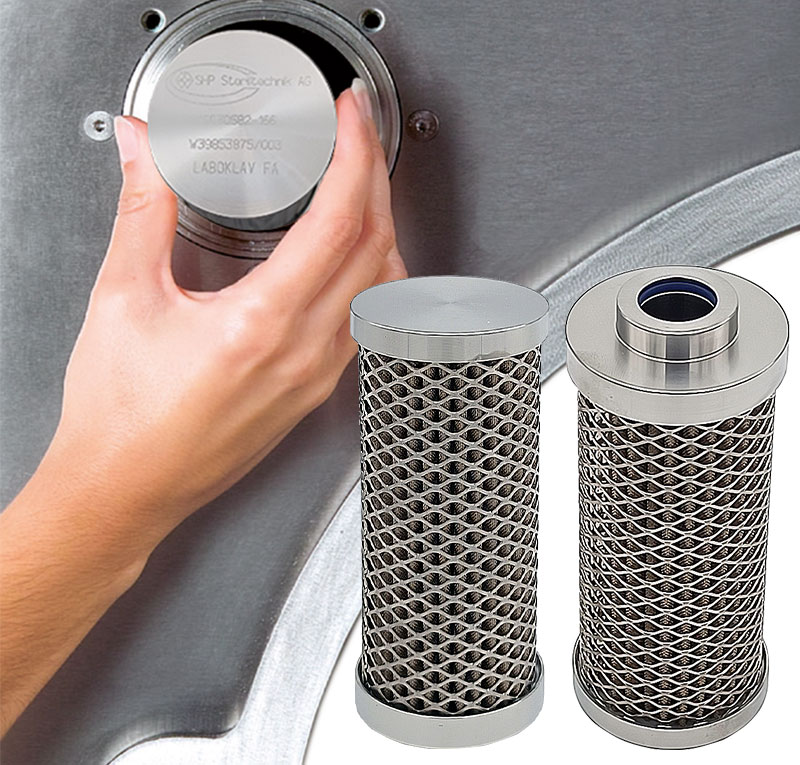
Exhaust air filtration – to protect the user and the environment
Sterilization of infectious or genetically modified materials makes special demands on the autoclaves. An exhaust air filtration system protects the user and the environment from dangerous germs that can enter the environment during deaeration of the chamber and allows the autoclaves to be used in safety level 2 laboratories or higher.
Exhaust air filtration includes sterilization of the condensate and temperature-controlled inline sterilization of the filter cartridge. A pressure-resistant stainless steel housing encloses the filter element and prevents the filter from expanding. We only use filter elements with manufacturer certificates. An integrated batch counter checks the filter element‘s service life and indicates when the filter should be replaced in accordance with the manufacturer‘s instructions.
The individual options are based on the current state of technology and the requirements of applicable laws, regulations, standards, and directives, including:
ArbSchutzG: Arbeitsschutzgesetz
ÜAnlG: Gesetz über überwachungsbedürftige Anlagen
BetrSichV: Betriebssicherheitsverordnung
DIN 58951-2:2018-01: Sterilization - Steam sterilizers for laboratory sterilization items - Part 2
DIN EN 61010-1 VDE 0411-1:2020-03: Safety requirements for ... laboratory equipment
Richtlinie 2014/68/EU: Pressure Equipment Directive
TRB 402: Equipment of pressure vessels, openings, and closures
TRBA 100: Protective measures for activities involving biological agents
GenTSV: Genetic Engineering Safety Ordinance